Not so long ago, you likely gawked at the sight of a 3D printed trinket. Out of a machine, you watched melted plastics get molded into something real and tangible. Interesting and creative, as with all new tech, 3D printing was a new hobby reserved for nerds making miniature plastic replicas of the Starship Enterprise. 3D printing failed to wow and was not the second coming of the wheel. In truth, besides the nerds of the world, few people paid attention to the shiny new technology.
But, times have changed, and people are starting to take notice – and will continue to do so as 3D technology expands its global presence. Today there are a variety of practical and useful applications in many fields thanks to 3D printing. Fields such as medicine, education, manufacturing, and art are currently taking advantage of 3D printing innovation. They're using the technology to accomplish production goals in record-breaking time, all while coming in under-budget. Now it seems the technology knows no bounds. Check out the exciting developments in the construction industry - residential houses.
3D Printed House for Sale Now – Not Coming Soon
A completed 3D house ready to occupy – sounds like a bit of fiction. Yet, in Riverhead, New York, an active listing already exists on the property mega-website Zillow. According to the 3D Printing Media Network, the listing is live now on the MLS, with more on the way. Not coming soon – here now.
And the finished product is no plastic trinket. The beautiful 3D home for sale in New York measures over 1400 square feet. It even includes a 2.5 car detached garage that adds another 750 square feet. The house's livable part includes three bedrooms and two full bathrooms, and it all rests on ¼ of an acre - all for only $299,999. Not impressed? Consider that comparable, non-3D homes in the area go for double the price – or more.
This innovation is thanks to SQ4D Inc. The company accomplishes the 3D feat by setting up their ARCS (Autonomous Robotic Construction System) on a building site in only 6 to 8 hours. From there, the ARCS takes over and begins systematic construction on many facets of the 3D home build.
How Much Does it Cost for a 3D Printed House?
Anyone looking to buy a new home in today's real estate market knows how high the cost can be. As demand for new homes increases, so do average prices. To compound the issue, traditional houses take much longer to manufacture versus a printed house. That means fewer new home inventories for the consumer with more cost added to what's available. 3D printing changes the game in a big way.
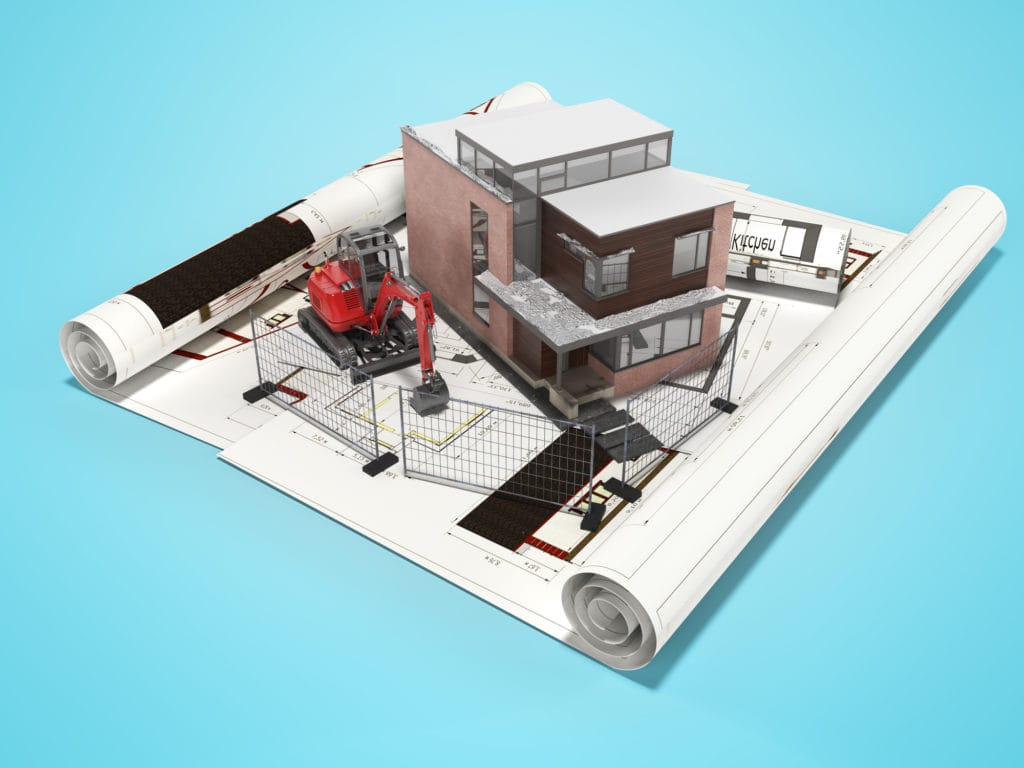
As seen in a recent CNN article, the printed house process means faster construction times versus traditional building. It comes with the bonus of being cheaper. In fact, up to 10% faster and 50% cheaper to build, according to Stephen King, the listing agent of the 3D home in Riverhead, New York. The proof, as they say, is in the pudding – or 3D home. For sale at only $299,999, the printed house compares with a standard built home listing at about $600,000. Talk about a tremendous bang for your buck.
Paying 50% less for a new home also means the market opens up to a whole new group of potential home buyers. Those unable to afford a new home at $500,000 may very well find $250,000 within their home purchasing budget. In a snap, the dream of homeownership becomes more attainable. Luckily printed houses get built faster. That means they're unlikely to add to the backlog in new home inventory that already exists.
What are 3D Printed Houses Made Of?
Thinking of something that is 3D printed might bring to mind something molded and created from cheap plastic. But when it comes to 3D homes, an amazingly strong material dominates the build – concrete. There are still some things done the old fashion way, such as doors and windows. But the concrete gets poured by huge 3D printers layer by layer. It forms everything from the footing, foundation, and even the walls of the 3D home build. In essence, the shell of the printed home is pure concrete.
Smaller structures do not limit this new way of building either. In Belgium, a company called Kamp C created the world's largest 3D printer to construct a two-story house, according to an article from Digital Trends. The project saw Kamp C create a massive gantry printer measuring an astounding 32 feet by 32 feet. The printer then made the 3D multi-floor structure using all concrete. Yet, the two-story printed house still boasts features such as heated flooring and solar panels. So 3D homes can be both innovative and sustainable.
How Long Will a 3D Printed House Last?
Buying a new home as opposed to one that is older means everything is, well, new. New brings peace of mind for a homeowner who can rest easy knowing nothing will be falling apart – at least at first. Many new homes do come with a home warranty. Several states enforce a guarantee on any new home built within their borders. But these guarantees often only last for up to 5 years.
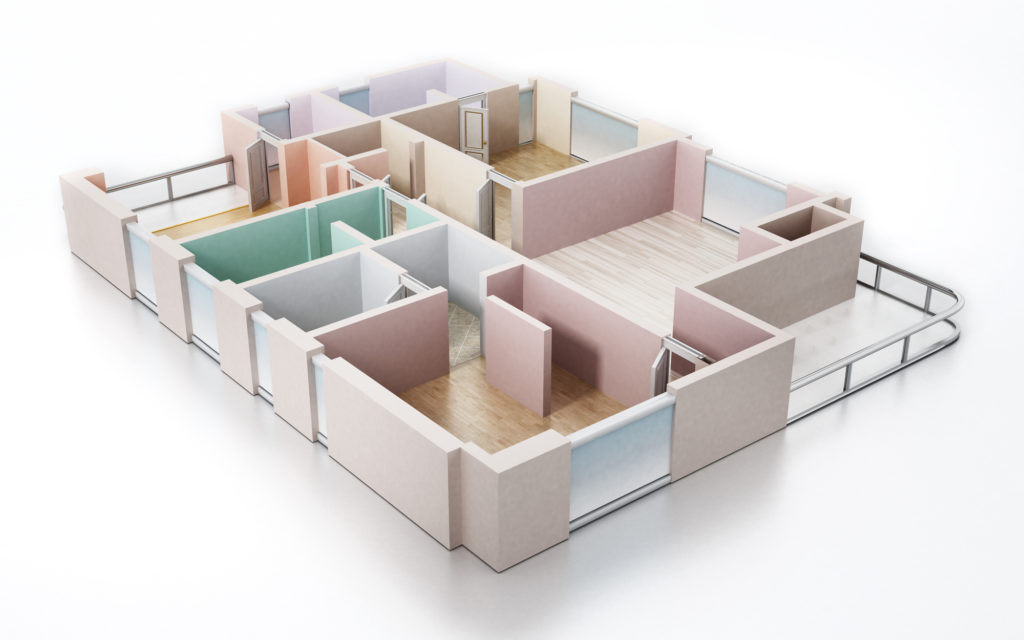
Once again the 3D housing market comes along to change the industry forever and for the better. SQ4D, the company that built the 3D house currently for sale in Riverhead, New York, offers a warranty that no traditional builder can beat. Ten years would be amazing and 20 years unheard of, but SQ4D truly backs their 3D projects with a full 50-year limited warranty. More than peace of mind, SQ4D is all but offering a lifetime guarantee.
Save the Day, The 3D Way
With the ability to economically build quality sustainable homes that will last, the printing of houses might just save the day. In any major metropolitan area, there are bound to be several affordable housing projects in the works. But when the term affordable gets thrown about, slashed costs often leave both quality and durability out of the equation. 3D homes being 50% less to manufacture, already have a sort of built-in cost-cutting device. This advantage would allow cities and states to save money without sacrificing any level of quality or durability.
Imagine people living in low-income housing that is not falling apart around them. Or taking homeless people off the streets and putting them in quality accommodations without breaking the state's budget. This accomplishment is thanks to the innovative minds behind 3D houses.
Printed Houses Looking to the Future
Albert Einstein once said, "We cannot solve our problems with the same thinking we used when we created them."
Einstein's statement rings true in home construction. Though some innovations have come along over the past several hundred years, home building ideas remain much the same. Materials and labor are increasing, if anything, as are costs. But homes are simply not built at a fast enough pace or an ultra-affordable price.
SQ4D has already proved that the future in homebuilding belongs to 3D. Having cracked the New York real estate market, arguably one of the country's most difficult, they have already set their sights on more. The company has building plans laid out from New York to California, and some are already in the construction phase. With lower costs and faster production, it makes sense that the real estate market must change with the innovation of the 3D home. Building a home that lasts may not be a new idea. But building a fast and affordable 3D home that lasts will prove to be the future.
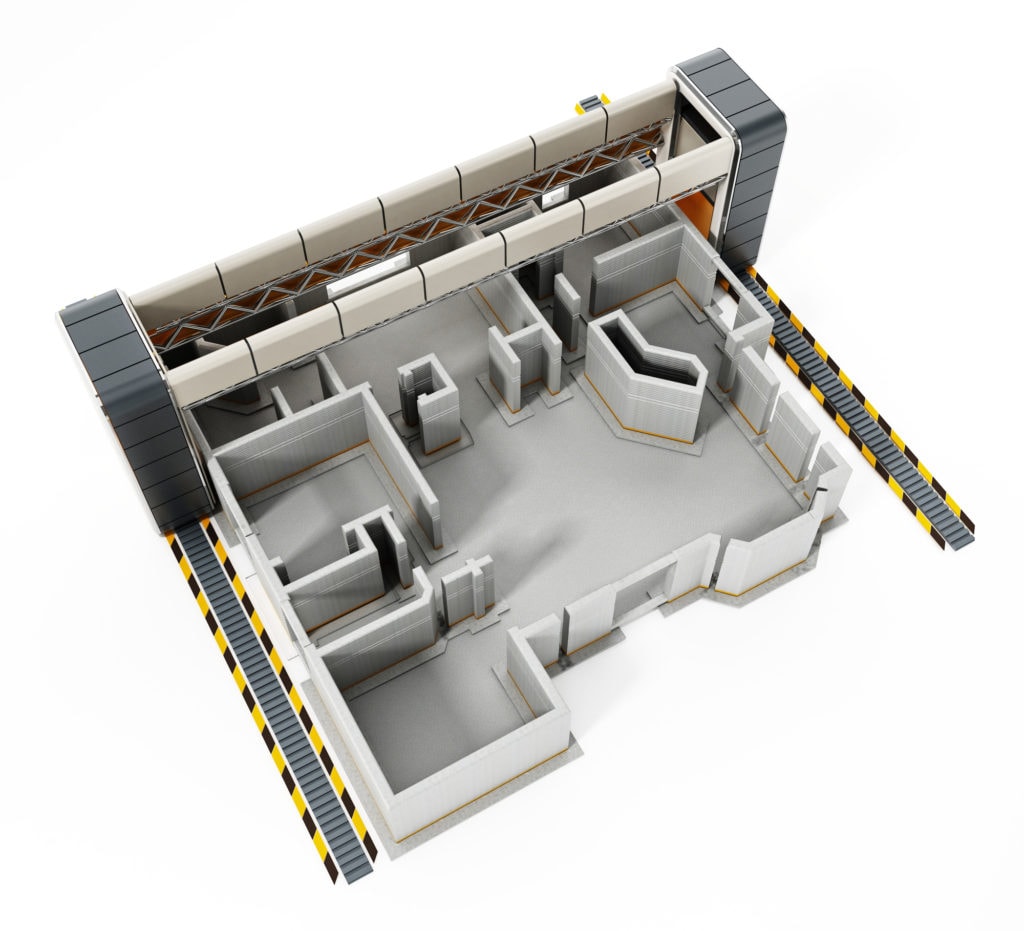
The Takeaway
Our world faces challenges our ancestors never foresaw. Affordable high-quality housing is one of the biggies. Even a couple of generations ago, home ownership was more easily obtainable. That’s why it’s no surprise that innovators and entrepreneurs would invest in the technology needed to solve that problem at scale.
The advent of the 3D printed house is just one example of how capitalism spurs advancements in technology to improve people’s lives. We look forward to watching this innovation unfold.
Years ago, when 3D printing technology was just a fantasy, someone had the idea and ran with it. They committed to solving a problem, then gathered the team and funding they needed to make this idea happen. Now, we talk about this capability as if we’d had it all along.
Whatever idea you have brewing in your brain, whatever problem you want to take on and solve to serve your fellow humans, we urge you to go for it. You don’t have to do it alone. There are more resources available than ever to help you get started. There’s never been a better time than now to build your business.